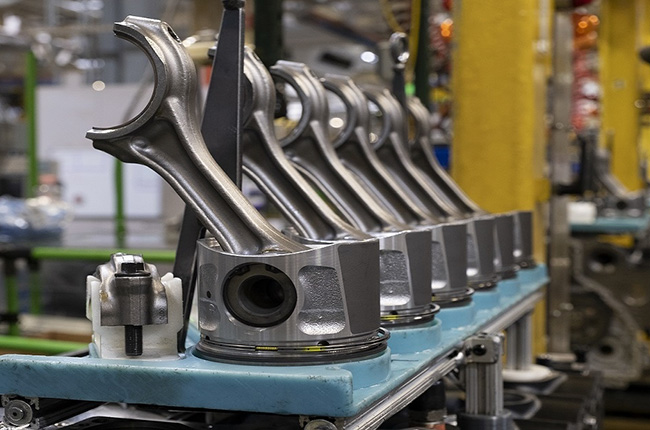
Cummins Inc., a renowned leader in global power and technology, has recently unveiled a groundbreaking achievement in collaboration with Oak Ridge National Laboratory (ORNL). They have successfully developed an advanced high-temperature steel alloy. This cutting-edge material is set to revolutionize Cummins' engines, enhancing their durability and overall efficiency. By incorporating this innovation, Cummins says it's aiming to better serve its customers through this new steel alloy. This development in Cummins’ engine building is quite important as some manufacturers here in the Philippines like Foton, use engines made by Cummins in their trucks.
Ever since its partnership with ORNL began in 2018, the collaborative project focused on exploring and advancing an alternative steel alloy has yielded remarkable outcomes. The primary objective was to create a cost-effective solution that offers exceptional resistance to high-temperature oxidation and increased strength. The research and development efforts have proven to be efficient, delivering swift and notable results.
“The partnership with Oak Ridge National Laboratory and development of the new material shows the serious potential for improvements and efficiencies for our engines. I am extremely proud of the value of work our team has provided and the future improvement it lends.”
Conventional materials utilized in the past have posed limitations on achieving significant improvements in engine efficiency and emissions reduction. These materials have hindered engineers from effectively extracting additional heat from the combustion process due to premature degradation caused by oxidation, scaling, and cracking.
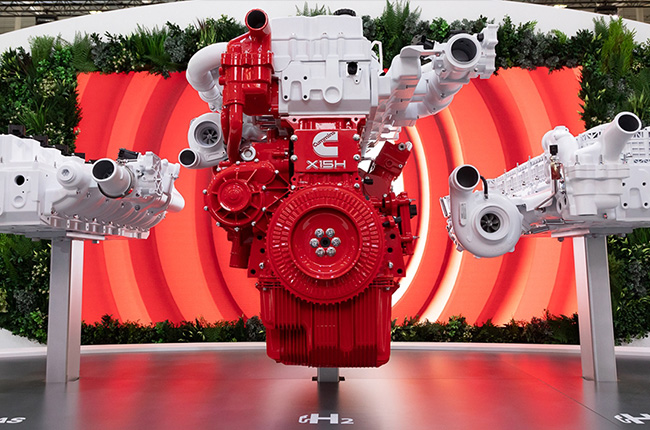
The recently developed material demonstrates remarkable strength at high temperatures, surpassing the commonly used commercial 4140 steel, while effectively eliminating the associated degradation pathways. In direct comparison to 4140 steel, the innovative alloy exhibits a significant 85 percent increase in Ultimate Tensile Strength (the maximum stress a material can endure while being stretched or pulled before breaking) and an impressive 143 percent enhancement in fatigue strength (the maximum cyclical stress the material can withstand for at least 10 million cycles before failure) at 600 degrees Celsius.
Furthermore, a rigorous and extended engine test was conducted using pistons made from the newly developed material. Remarkably, no instances of cracking were observed, and minimal occurrences of oxidation or scaling were recorded. Notably, this advanced material enables an impressive temperature capability increase of at least 50 degrees Celsius compared to the current 4140 steel in use.